Day 6 – Valmet Rautpohja
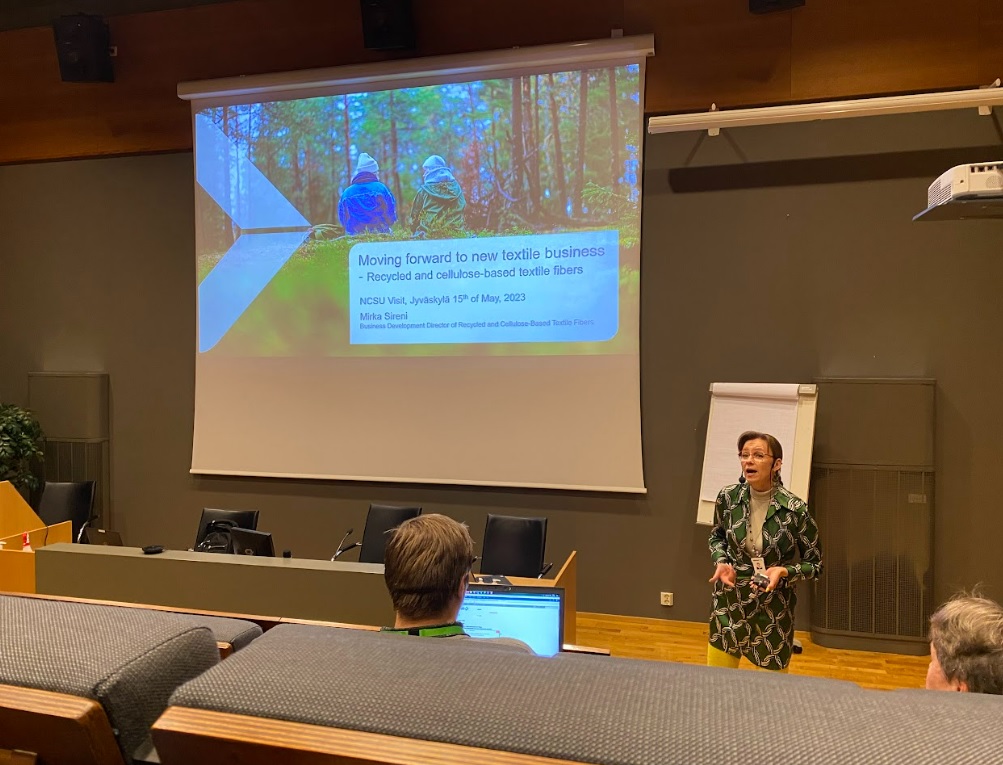
Day 6 – by Sky Johnson, Sophia Mills and Josh Carter
On our final full day in Jyväskylä, we toured Valmet’s Rautpohja facility here in the town. This facility is home to some of Valmet’s top research for improvement in the papermaking process as well as their design center for some of the equipment that they make for their customers in order to assist with their issues on the line.
We arrived around 8:15 am where we were met by Reijo, our contact from Valmet who has accompanied us previously on multiple tours the past week. He welcomed us to the Rautpohja facility and brought us into the auditorium in the main building, where we were given a brief presentation about the facility itself and safety guidelines for the mill, and then groups B and C were taken on a tour of the facility while group A listened to a presentation. After groups B and C concluded their tours, group A went on tour while groups B and C listened to the presentation.
At this facility, Valmet uses process information that they receive from their customers to design machinery that will fit their customer’s specifications. From the time that the customer gives Valmet their request to the time when the customers receive the final product is about a three-year process. They start by making 3D models of the mill’s process equipment and designing the requested machinery to fit. Once the design process has been completed, they begin ordering the raw materials for the production process as well as the parts that they will not be making themselves. As one of the guides for the tour, Jose, told us, if there are any parts smaller than a horse that is needed, they will be ordered rather than made at the facility. The larger parts are machined in the house using a variety of equipment and each of the parts is machined to a very high tolerance, about 33 micrometers. The parts are ground and polished manually because according to the technicians, nothing is as accurate as the human eye. After the parts have been completed, the whole thing is assembled in the shop to ensure that the parts fit together perfectly, is labeled to ensure that all the parts are present and make it to the customer, and are then shipped to the customer to be assembled at the mill with the help of another Valmet specialist.
During our time at Valmet, we listened to five different presentations. After the aforementioned presentation about Valmet’s history and global presence, we listened to after our tours; we were treated to a presentation on 3D fibers by speaker Sampo Immonen, which covered the new molded fiber technology as a replacement for plastics. The technology used to create these molded fibers is set up in modules, allowing each site to decide what parts they actually need and letting them remove or add modules as the process decides. Although the size is subject to change depending on the needs, it only has an average length of 32 meters, as opposed to a liner machine, which can be 175 meters long.
We then learned about the textile business with Mirka Sireni, and how, despite being the 3rd largest industry in the world, 73% of textile fibers are either incinerated or landfilled, instead of recycled. She further went into how there are low collection rates due to various issues, the difficulty in separating the textiles, as well as the current impossibility of re-spinning recycled fibers. Although there is much research needed to be done in order to accomplish better recycling rates of textiles, there are still improvements on the governing and social side, specifically with the EU enforcing the placement of convenient textile recycling bins across Europe by 2025.
Afterward, Markku Markkanen presented on the Industrial Internet. The key takeaway was the switch from employees needing to be on-site all the time when most work could be done remotely, which became clear during the Covid-19 pandemic. The most impressive tool to allow this at-home work style is the Valmet Virtual Mill, which will give a hands-on experience to the workers in a virtual reality simulation of the site.
Finally, we ended the day with Jukka Muhonen’s presentation on Aalen PM5. Aalen PM5 is a new paper machine concept that uses various kinds of Valmet technology in order to run a low base weight of Palm Ultra. Light Corrugated Case Material. This kind of low-basis weight material requires high retention, gentle drying, and minimized draws in order for the machine producing it to run most effectively. Valmet’s Aalen PM5 is a very cleanly machine with high speeds and low energy consumption, running around 1800–2000 meters per minute with a steam economy of 1.1 pounds of steam consumed for every pound of paper the machine produces. Our day concluded at the Ranssi Inn, where we got to experience the smoke sauna and eat a wonderful Finnish dinner at the restaurant.
- Categories: